Introduit en 2003 par le docteur Michael Grieves (enseignant à l’université du Michigan), le terme jumeau numérique (ou « digital twin ») est désormais très utilisé dans certains secteurs comme la construction ou l’immobilier. Le monde de la santé est lui aussi en train de découvrir le concept grâce à Dassault Systèmes. L’entreprise souhaite en effet, développer un jumeau numérique du corps humain pour comprendre, modéliser, examiner, tester et traiter avec précision les interventions médicales sur un modèle virtuel. Dans l’industrie, les jumeaux numériques existent depuis plusieurs années mais la marge de progression est encore importante. Au vu des bénéfices apportés par ces reproductions virtuelles, il serait en effet dommage de s’en passer.
L’industrie, terrain de jeu privilégié pour les jumeaux numériques
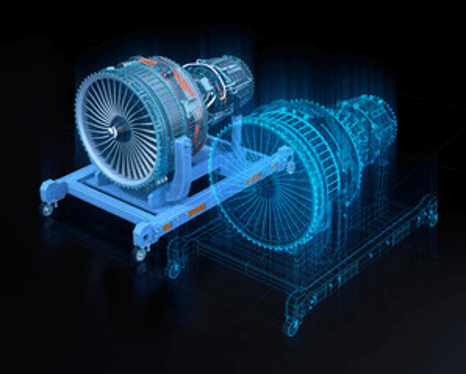
Un exemple parlant du concept de jumeau numérique est celui d’Apollo 13. Lorsqu’en 1970 l’équipage alertait les membres du projet d’un problème, c’est en grande partie grâce à la réplique de la navette et de ses composants que le sauvetage fut un succès.
50 ans plus tard, les jumeaux numériques sont partout, notamment dans le monde industriel… Nombreux sont les ingénieurs dans l’aéronautique, l’automobile ou encore le nucléaire, à modéliser des jumeaux numériques pour leurs projets. Cependant, ce merveilleux outil est malheureusement moins démocratisé dans l’industrie que dans le bâtiment par exemple. Pourtant, c’est bien dans ce domaine que le retour sur investissement est le plus important. Comparer le « tel-que-construit » au « tel-que-conçu », illustrer et documenter les phases d’assemblage, etc. Les possibilités offertes sont nombreuses et apportent des gains de performance majeurs.
Les jumeaux numériques les plus aboutis permettent en effet aux ingénieurs d’avoir accès à des représentations exactes d’actifs physiques. Avec la simulation, ils peuvent ensuite faire des recommandations pour les futures conceptions ou pour l’entretien. C’est d’ailleurs ce qu’a fait Renault en utilisant un jumeau numérique de son outil de production pour optimiser sa production de moteurs. Avec une véritable cartographie, représentée sous forme d’organigramme dynamique, des postes clés de l’infrastructure de production et de leurs interconnexions, Renault a pu identifier les goulots d’étranglement dans les flux et apporter les corrections nécessaires. Le groupe souhaite maintenant aller plus loin en intégrant plus de données car un jumeau numérique est d’autant plus efficace s’il est bien alimenté.
Un allié de choix pour la maintenance prédictive
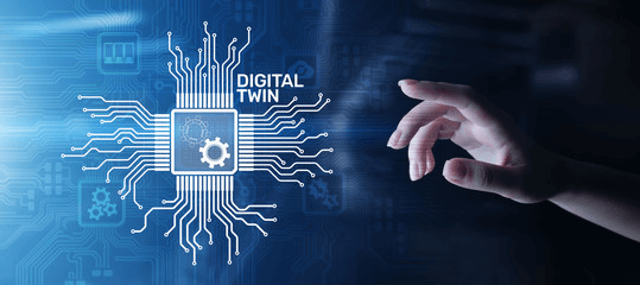
Les constantes avancées dans l’internet des objets sont d’excellentes nouvelles pour tous les projets de « digital twin » pour de la maintenance prédictive. Afin de rester concret, prenons l’exemple des éoliennes. On en décompte environ 216 000 actives de par le monde. Sur ce parc, près de 38 000 incidents sont dénombrés chaque année. Au Royaume-Uni une entreprise a donc assigné un jumeau numérique à chaque éolienne du territoire, alimenté par l’IoT, afin d’adapter au mieux la maintenance et prolonger leur durée de fonctionnement. Résultat ? Une économie de 47% par rapport à de la maintenance réactive.
En France, nous pouvons prendre l’exemple de Schneider Electric, qui compte parmi les entreprises les plus avancées dans l’utilisation de jumeaux numériques. L’entreprise modélise par exemple ses installations Microgrids (dispositif conçu pour fournir de l’électricité issue de différentes sources avec un objectif d’efficacité énergétique). Grâce à cela, il est possible d’optimiser la maintenance du parc de matériel mais aussi l’utilisation d’énergie avec la simulation en fonction de certains évènements comme les pics de consommation, le climat, etc. L’efficacité des jumeaux numériques a amené le groupe à les déployer dans d’autres cas grâce à un groupe de travail dédié, d’une dizaine de personnes. Ce travail est rendu possible notamment grâce au MBSE (model based system engineering) aujourd’hui utilisé dans tous les départements. Puisque la grande majorité des produits passent par une phase de conception numérique dès le design, il est ensuite plus rapide de concevoir les jumeaux numériques.
Les acteurs de la supply chain suivent eux aussi de très près les avancées des technologies « digital twin ». En répliquant virtuellement les entrepôts, les usines ou les chaînes de production, il est possible d’économiser beaucoup de ressources. Grâce à une démarche « What if », il est en effet possible de déterminer les impacts d’une décision stratégique puis de prendre les mesures nécessaires grâce à la démarche « How to ». C’est ce que Renault, dont nous parlions dans la partie précédente, a mis en place.
Chez KAIZEN Solutions, nous accompagnons de nombreux clients dans la mise en place de projets « digital twin ». Si vous souhaitez en savoir plus, échanger autour des projets que nous avons déployés, réaliser un POC, ou pour toute autre demande, n’hésitez pas à nous contacter !
Contactez-nous
Retour aux articles